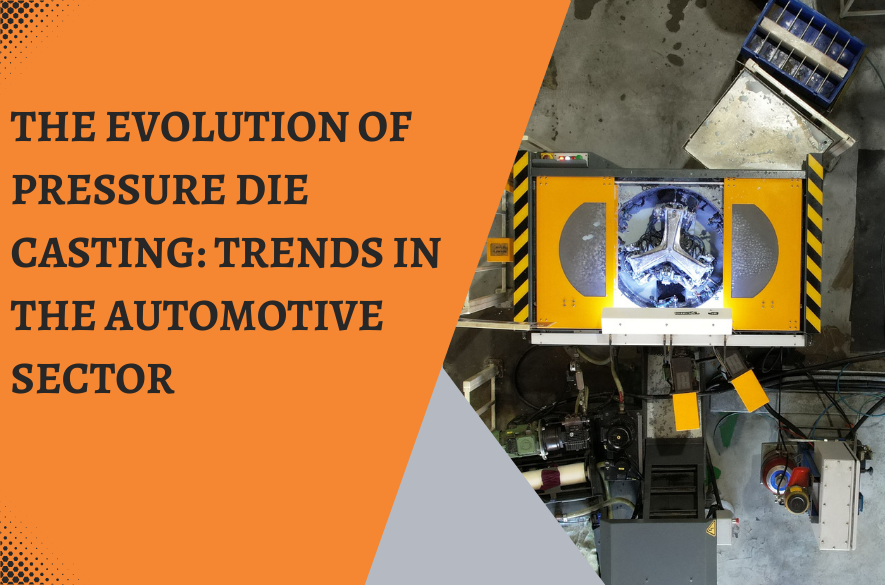
The Evolving Landscape of Pressure Die Casting in Automotive Manufacturing
Pressure die casting has long been a cornerstone of the automotive industry, offering precision, strength, and efficiency in the production of critical components. As the industry transitions towards lighter, more fuel-efficient, and technologically advanced vehicles, the evolution of die casting continues to play a pivotal role.
The Rise of Aluminum
One of the most significant shifts in recent years has been the increasing adoption of aluminum die casting. Aluminum's unique blend of strength, corrosion resistance, and lightweight properties makes it an ideal choice for a wide range of automotive applications. From engine blocks and transmission cases to suspension components and structural elements, aluminum die casting enables manufacturers to achieve superior performance while reducing vehicle weight and improving fuel economy.
High-Pressure Die Casting: Precision and Speed
High-pressure die casting (HPDC) has emerged as a dominant force, driven by the automotive industry's relentless pursuit of high precision and rapid production. HPDC leverages significantly higher pressures to inject molten metal into the die cavity, enabling the creation of intricate parts with minimal tolerances. This precision is crucial for meeting the demanding requirements of modern vehicles, where even minor variations can impact performance and reliability.
Technological Advancements Shaping the Future
Several key technological advancements are further propelling the evolution of die casting:
- Simulation and Modeling: Sophisticated software tools enable engineers to simulate the entire die casting process, optimizing parameters, predicting potential defects, and accelerating product development.
- Automation and Robotics: Increasingly sophisticated automation and robotics are streamlining production processes, enhancing efficiency, and improving safety.
Sustainability: A Growing Imperative
Sustainability is rapidly becoming a key driver in the automotive industry, and die casting is no exception. Manufacturers are increasingly focused on:
- Energy Efficiency: Implementing energy-efficient equipment and processes to reduce their environmental footprint.
- Recyclable Materials: Utilizing recycled aluminum to minimize waste and conserve resources.
At Roots Cast Private Limited, we are constantly working on reducing the carbon emission and increasing the utilization of green energy in the production process as a step to create a sustainable environment.
Addressing the Challenges
While the future of die casting in the automotive industry appears bright, several challenges remain:
- Meeting Stringent Emissions Regulations: The industry faces increasing pressure to comply with stringent emissions regulations, necessitating the development of lighter, more efficient components.
- Maintaining Quality and Consistency: As parts become more complex and demanding, ensuring consistent quality and minimizing defects remains a critical challenge.
- Staying Competitive: The global market for automotive components is highly competitive. Die casters must continuously innovate and improve their processes to remain competitive.
Conclusion
The evolution of pressure die casting mirrors the dynamic needs of the modern automotive sector. By embracing advancements in materials, processes, and technologies, while addressing the challenges of sustainability and competition, die casting will continue to play a vital role in shaping the vehicles of tomorrow. At Roots Cast, we majorly produce die cast components for automotive sector.