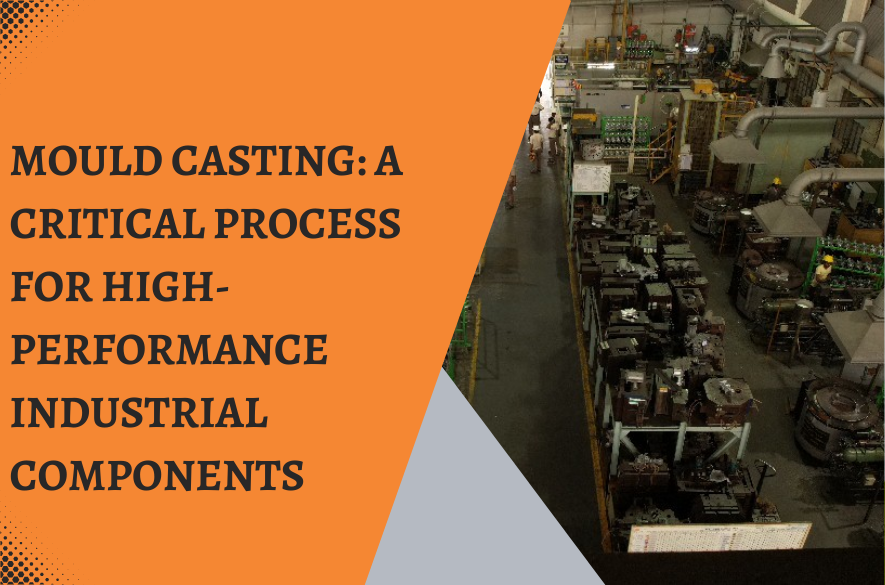
Mould Casting: A Critical Process for High-Performance Industrial Components
Mould casting is an essential technique used in the production of high- performance industrial components. It is a process by which intricate designs can be made with accuracy and tolerance. This process finds wide application in industries such as automotive, aerospace, railways, medical and general engineering.
What is Mould Casting?
The mould casting procedure involves pouring hot molten metal into the cavity of a mould, allowing it to solidify into the required shape. The mould is generally made up of high strength material as it has to resist the temperature and pressure of poured molten metal. Mould casting is especially suitable for the production of geometrically complicated parts with high surface quality and also ensures high mechanical properties, accuracy, and precision of the part.
Types of Mould Casting
1. High-Pressure Die Casting (HPDC): HPDC involves the injection/forcing of molten metal into a mould cavity at high pressure, also called Intensification pressure. It is amazingly effective in the manufacturing of a large volume of small to medium-sized parts that boost production rate, excellent dimensional accuracy, and surface finish. Roots Cast, one of the leading aluminum die casting manufacturers in India-uses a range of HPDC machines ranging from 120 tons to 1400 tons capacity to cast components ranging from 200 grams up to 10 kg (0.6 lbs to 22 lbs) and also pressure die casting machines are equipped with automatic alloy ladling, robotic casting extraction and IOT - System Integrated facility.
2. Gravity Die Casting: Contrary to HPDC, GDC relies on gravity to fill the mould with molten metal. Gravity Die Casting is very suitable for casting heavier components with high wall thickness, offering better mechanical properties compared to other methods of casting. Roots Cast utilizes the various machines in GDC, such as tiltable gravity die casting machines and horizontal clamping machines, to produce castings with weights ranging from 150 grams up to 75 kg (1.30 lbs to 165 lbs).
3. Low-Pressure Die Casting: LPDC works based on applying low pressure inside the sealed furnace containing molten metal to fill the mould through riser tubes, ensuring the controlled filling and restricted turbulence. This method enables us to get quality castings with minimal defects. Roots Cast uses a fully automatic LPDC machine, which includes a 500 furnace and air, water & mist cooling lines, which enables the production of components weighing from 500 grams to 35 kg (1 lb to 77 lbs) with strict metallurgical standards.
The Role of Aluminium Die Casting Manufacturers
Roots Cast is one of the leading aluminium die casting manufacturers, playing a crucial role in the die casting industry by providing custom-fit casting solutions to various OEMs and tier-I customers. We provide one- stop solutions, starting from tool design and manufacturing, die casting, machining, and surface finishing of the products and sub-assemblies. RCPL ensures that they meet each customer's exact requirements and global quality standards.
Casting Manufacturers of India: Meeting the Global Standard
The Indian casting manufacturers have evolved a lot in the implementation of advanced technology and quality management systems. Roots Cast ensures that they follow international standards in every stage of operation. This reflects the commitment we have towards quality and precision.
Conclusion
Mould casting continues to be a critical process for the manufacturing of high-performance industrial components. With the continuous advancement in technology and improved capability for manufacturing, aluminium die casting manufacturers in India continue to raise new benchmarks in quality and efficiency to cater to diverse industries worldwide.