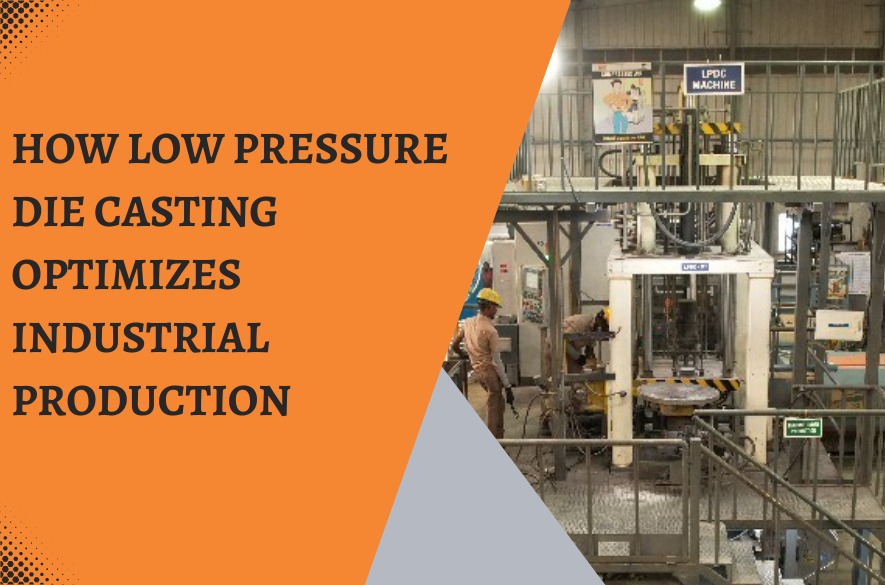
How Low-Pressure Die Casting Ensures Higher Efficiency in Industry Production
In modern manufacturing, efficiency is the key to success. One of the most effective techniques used to enhance production quality and output is low-pressure die casting. This method has revolutionized the way metal components are produced, making it a preferred choice among aluminium die casting manufacturers and other industry players.
What is Low Pressure Die Casting?
LPDC is a casting process where molten metal is injected into a mold cavity under low pressure. This controlled and gentle approach distinguishes it from high-pressure die casting, which utilizes significantly higher forces. The low-pressure environment minimizes turbulence during the filling process, leading to superior casting quality. This makes it an ideal choice for manufacturing high-integrity components such as safety components, alloy wheels, etc., and in sectors like automotive, aerospace, and industrial machinery.
Key Efficiency Benefits of LPDC
Higher Material Utilization
Low-pressure die casting results in minimal material wastage, hence reducing the overall production cost for die-casting companies. It also allows for better metal recovery, making it a more sustainable option.
Better Product Quality
Low-pressure die casting produces components with fewer porosities and higher mechanical strength due to reduced turbulence. This is very important for industries that demand precision and durability, such as automotive and aerospace manufacturing.
Energy Efficiency
Compared to traditional high-pressure die casting methods, LPDC is much less energy-intensive since its operating pressure is much lower. This results in huge energy saving over time.
Consistent Production
The filling process in LPDC is very controlled, meaning the component structures will be consistent, and that improves reliability with reduced secondary machining processes.
Rising demands for high-quality metal components are forcing top aluminum die-casting manufacturers to include LPDC to maintain their momentum. Roots Cast, uses this technology to deliver superior products while promising efficiency and sustainability.