Sub Assembly Facilities
Sub Assembly Facilities and Assembly Lines
As one of the leading die casting companies, Roots Cast (RCPL) provides complete sub-assembly facilities and assembly lines to cater to the diverse demands of our customers. Our world-class infrastructure and latest technologies ensure that we provide quality die casting products and sub-assemblies with precision and efficiency.
Sub Assembly Facilities
The main sub-assembly line is planned for a wide-range, complex task with various high-precision components to be used. Our assembly lines are well-designed with the latest equipment and technology to ensure the integration of multiple parts in each line. Our lines specialize in creating strong and reliable sub-assemblies that meet the strict quality requirements of their clients.
Sub-Assembly Lines
We have designed and developed our assembly lines in a manner that allows us to have maximum efficiency with Poka-Yoke to prevent defects. We assemble parts using robust equipment and automated processes very efficiently and accurately. We develop and assemble the following child parts with our castings:
- Springs: To serve various mechanical functions accurately, we incorporate springs into our assemblies.
- Rubber Components: This is achieved through quality rubber parts used to ensure the absolute performance and resilience expected.
- Sheet Metal: Our sheet metal parts are as well developed with precision to meet the exact dimensions and specifications of the clients.
- Plastic Components: Our assemblies are incorporated into strong plastic parts that enhance functionality for a minimal amount of weight.
- Turned Parts: Precision-turned parts are essential to the smooth working of our assemblies.
- Fasteners: We will utilize high-quality fasteners to make sure our assemblies are strong and reliable.
Quality Assurance
Our sub-assemblies undergo extensive quality check procedures that include the following:
- Leakage Test: In this test, we ensure that our assemblies have no leaks so that they do not play a spoilsport while performing their work.
- Priming Test: We confirm that the pump and other components have been primed properly to work at their top speed.
- Functional Test: Functional test confirms whether the assembly is working as it is required to perform under various conditions.
- Shut Off Pressure Test: Here, we check the possibility of shutting it down and performing under high-pressure conditions for the tested assembly.
Assembly lines
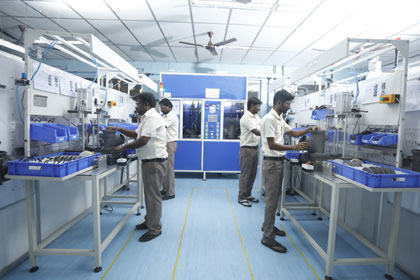
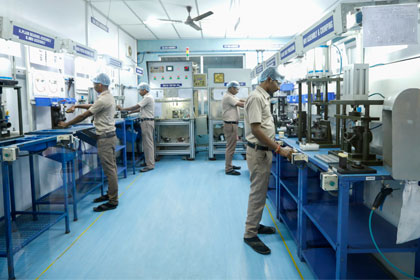
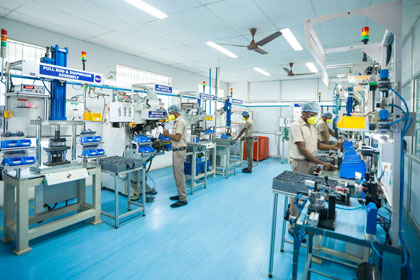
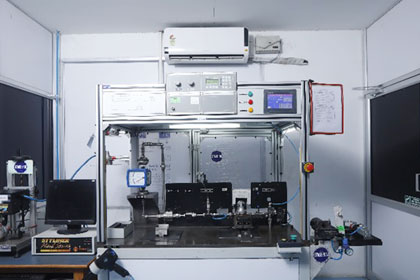
Consists of 52 child parts includes
- 4 Al. Die Cast
- Spring
- Rubber
- Sheet metal
- Plastic
- Turned parts
- Fasteners
Pump is passing through
- Leakage test
- Priming test
- Functional test
- Shut Off pressure test
DIAPHRAGM FUEL PUMP FOR PISTON-OPERATED AIRCRAFT ENGINE
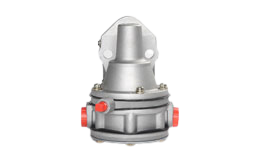
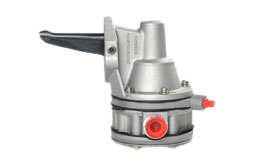
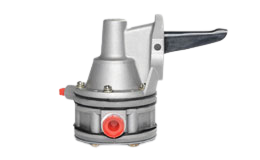
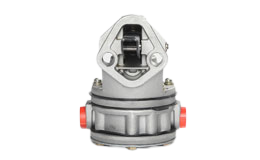