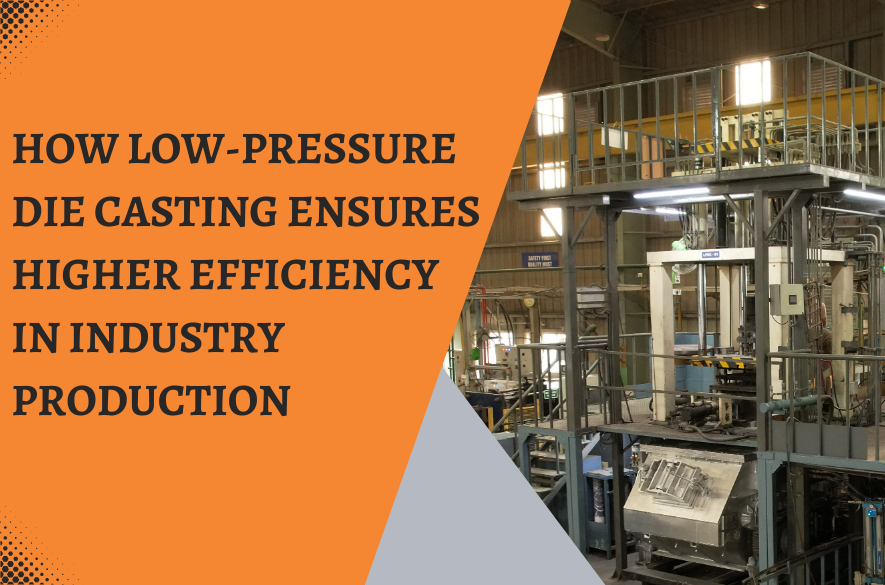
How Low Pressure Die Casting Optimizes Industrial Production
In modern manufacturing, achieving both precision and efficiency is paramount. Low-pressure die casting (LPDC) has emerged as a leading technique, particularly for aluminum components, offering significant advantages over other casting methods. This process is increasingly favored by manufacturers seeking to optimize production and enhance product quality.
Applications Across Industries
Roots Cast applies Low-pressure die casting in various segments like,
- Automotive: They manufacture engine blocks, cylinder heads, wheels, brake components, and structural parts for the automotive industry.
- Aerospace: They produce aircraft engine components, landing gear parts, and structural components for the aerospace industry.
- Industrial Machinery: They manufacture pump housings, valve bodies, gearboxes, and hydraulic components for industrial machinery.
- General Engineering: They produce architectural hardware, plumbing fixtures, and lighting components for general engineering applications.
- Defense: They manufacture ammunition components and military vehicle parts for the defense industry.
Conclusion: A Powerful Manufacturing Solution
Low-pressure die casting offers a compelling combination of efficiency, quality, and cost-effectiveness. Its ability to minimize material waste, enhance surface finish, improve structural integrity, and streamline production makes it an increasingly important process in modern manufacturing. Roots Cast has state of an art low-pressure die casting production facility that uses digital proportional controlled Air/Water/Mist cooling lines to produce castings from 500 g to 35 kg. For companies seeking to optimize their operations and produce high-quality components, LPDC presents a powerful solution.