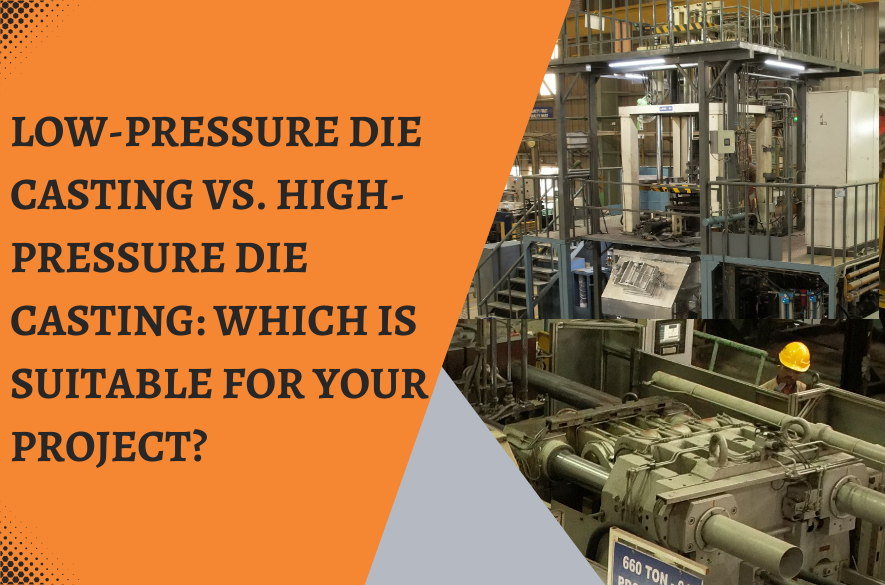
Low-Pressure Die Casting vs. High-Pressure Die Casting: Which is Suitable for Your Project?
For choosing the best die casting process for your project or to implement on your project we should understand the difference between low-pressure die casting and high-pressure die casting. Both methods are common within various industries, and they differ primarily in the applied pressure during casting.
What is Low-Pressure Die Casting?
Low-pressure die casting uses low air pressure (0.20 bar to 1.00 bar) to force molten metal into a die. Molten metal is held in a furnace below the die. Pressure forces the metal up a riser tube into the die cavity. Pressure is maintained during solidification. This method produces high-quality castings with good dimensional accuracy. It's often applied in making automotive alloy wheels, engine blocks, and structural components where strength is a requirement. Automotive, Aerospace, Marine, Industrial and heavy equipment manufacturing and Architectural industries are the major industries that adopt the LPDC method. At Roots Cast, we produce LPDC components weighing from 300 g to 35 kg.
Advantages of LPDC:
- Superior Quality: Minimal porosity, high density, and excellent surface finish.
- Precision and Consistency: Accurate dimensional control and repeatability.
- Cost-Efficiency: Lower scrap rates and less post-processing.
What is High-Pressure Die Casting?
High-pressure die casting is a rapid metal casting process where molten metal is injected into a reusable mold under extremely high pressure (typically 689.48 bar to 1378.95 bar). This high pressure allows for the creation of complex parts with intricate details, thin wall sections, and excellent dimensional accuracy. Automotive, Aerospace, Electronics, Consumer Goods, Medical Devices industries are the major industries that adopt HPDC method. At Roots Cast, we produce HPDC components weighing from 120 g to 7.5 kg.
Advantages of HPDC:
- High Production Rates: Rapid filling of molds, reducing cycle times.
- Complex Shapes: Creates intricate designs with thin-walled sections.
- Dimensional Accuracy: Tight tolerances, minimal need for machining.
Which Process Fits Your Project?
The decision between LPDC and HPDC depends on your project's needs: If structural integrity and durability are key, LPDC is the better choice and is suitable for mid volume products. For high-volume production and complex designs, HPDC is ideal. We at Roots Cast specialize in both Low-Pressure Die Casting and High-Pressure, providing tailored solutions to meet your project's needs.
Conclusion
The die casting method you choose can have a huge impact on the quality and cost-effectiveness of your project. Evaluate your needs carefully and collaborate with trusted experts to achieve the best results.