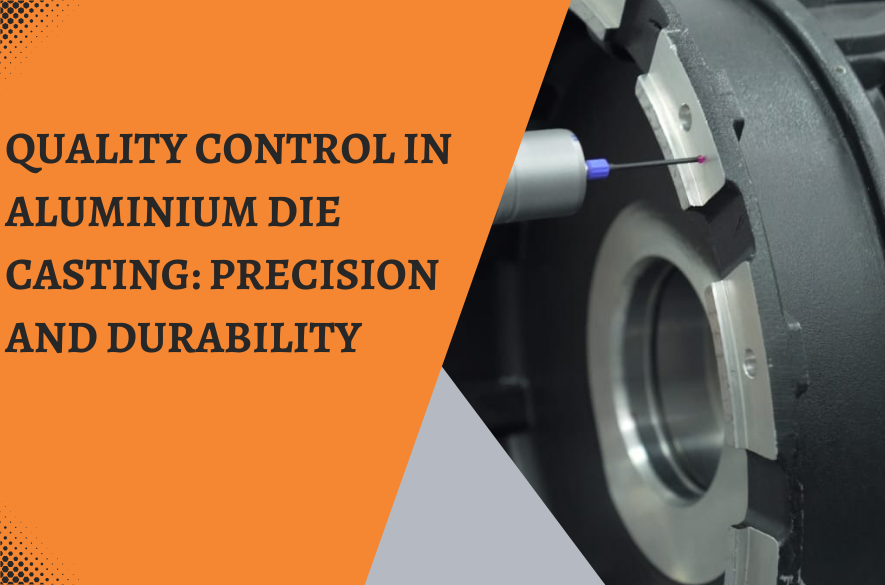
Quality control in aluminium die casting: Precision and Durability
Quality control in aluminum castings is a critical aspect of the manufacturing process, ensuring that the final products meet the required standards of quality, safety, and performance.
Testing and Inspection of Materials
The quality control process for aluminium die casting begins with an inspection of raw materials. Aluminium alloys are thoroughly tested to ensure they meet specific criteria for chemical composition, strength, thermal resistance, and durability. This proactive approach minimizes the risk of producing components that fail to meet the performance of the product.
Measurement and Dimensional Accuracy
Dimensional accuracy is critical from the outset of the aluminium die casting process to ensure that all manufactured parts conform to the intended design requirements. Measurement tools like coordinate measuring machines (CMMs) are employed to verify that components achieve the necessary level of precision. This meticulous approach guarantees compatibility within parts and minimizes material waste, both of which are crucial factors for aluminum casting.
Surface Quality and Structural Integrity
To assess surface quality and structural integrity, aluminum die castings undergo non-destructive testing methods such as X-ray and spectro analysis. These techniques effectively identify internal flaws or surface defects like porosity and cracks. By eliminating defective components from the production line, aluminium casting companies can consistently deliver reliable parts.
Process Automation for Consistency
Automation is a crucial element in achieving consistent quality in aluminium die casting. By automating factors like temperature, injection speed, and pressure, casting processes become more stable and repeatable. This reduction in human error leads to the production of high-quality products that meet stringent tolerance requirements.
Process Automation for Consistency
Automation is a crucial element in achieving consistent quality in aluminium die casting. By automating factors like temperature, injection speed, and pressure, casting processes become more stable and repeatable. This reduction in human error leads to the production of high-quality products that meet stringent tolerance requirements.
Continuous Improvement for Better Standards
Quality control is founded on the principle of continuous improvement. By analyzing feedback from quality checks, businesses can refine processes to enhance efficiency and elevate product standards. This approach empowers aluminium casting companies to consistently meet evolving customer needs while maintaining exceptional product quality. At Roots Cast, quality control is essential, and we use strict measures in aluminium die-casting to ensure our clients end up with components that meet their requirements.
Key Quality Control Techniques in Aluminium Castings:
- Visual Inspection : This is the most fundamental technique, involving a thorough examination of the casting's surface for visible defects like cracks, porosity, or misruns. Magnification tools and specialized lighting can enhance the detection of finer defects.
- Dimensional Inspection : This ensures that the castings conform to the specified dimensions and tolerances. It involves using measuring instruments like callipers, micrometers, and coordinate measuring machines.
- Metallurgical Analysis : This technique examines the microstructure of the casting to assess its internal quality, including grain size, porosity, and the presence of any defects or inclusions.
- Mechanical Testing : This involves subjecting the castings to various mechanical tests like tensile testing, impact testing, and hardness testing to evaluate their mechanical properties.
- Non-Destructive Testing (NDT) : NDT techniques like X-ray radiography, Spectro analysis, and ultrasonic testing are used to detect internal defects without damaging the casting.
- Statistical Process Control (SPC) : SPC involves the use of statistical methods to monitor and control the manufacturing process, identifying and addressing potential quality issues before they lead to defects