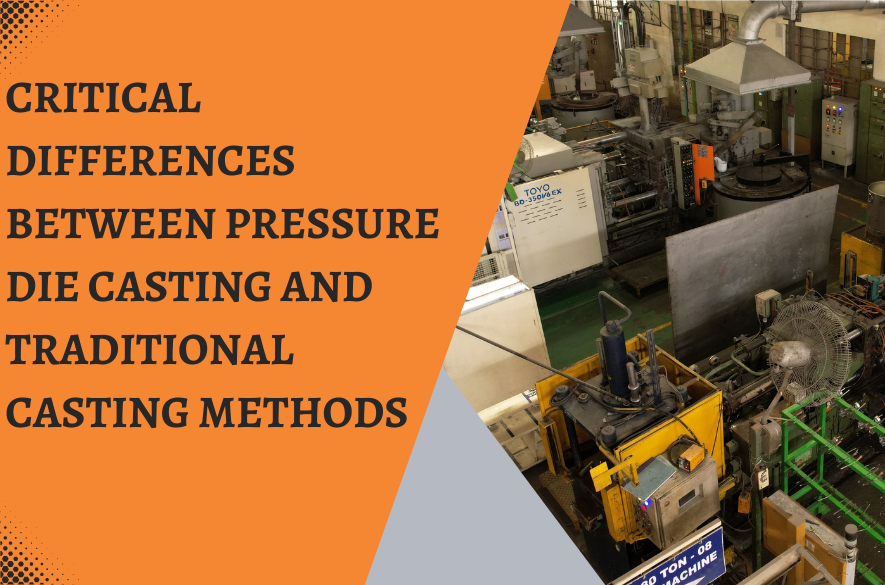
Critical Differences Between Pressure Die Casting and Traditional Casting Methods
Die casting has been considered one of the advanced manufacturing processes. How does pressure die casting compare with traditional casting methods? To explore the distinctions, let's talk about key differences and innovations.
Material Specificity
- Pressure Die Casting: This process is meant for aluminium and its alloy, which are highly corrosion-resistant and very lightweight. This application is more suited for the automotive, aerospace, and electronics sectors.
- Traditional Casting: This could range from sand casting, investment casting, etc. Its application can be carried out on anything, such as steel and iron, but when focusing on aluminium, it may not be so effective.
Casting Method
- Pressure Die Casting: The molten Aluminium is injected under pressure into a mould, and rapid solidification is carried out. In Pressure Die Casting, resulting parts get a finer surface finish and dimensional accuracy.
- Traditional Casting: Sand casting and others depend on gravity and basic moulds, which require post-processing and deliver lower accuracy and more ragged surface finishes.
Accuracy and Complexity
- Pressure Die Casting: The process delivers high accuracy with thin walls and lends itself to complex geometries with tight tolerance. High pressure in pressure die casting especially accounts for complex geometries.
- Traditional Casting: Although able to produce the part with complex details, traditional methods tend not to be as accurate and usually require more finishing work.
Production Efficiency
- Pressure Die Casting: The Pressure Die Casting process permits faster speeds and efficiency, especially in high volumes, and consequently lower unit cost.
- Traditional Casting: Much slower, especially taking into account mold preparation and time allowed for each cast to cool, and therefore less efficient and labor intensive for large-scale production.
Surface Finish and Strength
- Pressure Die Casting: It gives a good surface finish. This generally prevents post-casting machining operations to a greater extent. It can also achieve strength-to-weight ratios as the metal flow and density are significantly better.
- Traditional Casting: Methods like sand and investment casting often result in a coarser surface finish. Post-casting machining is necessary to make the surface smooth, and the strength might not be comparable to that of a pressure die-cast component.
Conclusion
When Pressure Die Casting is compared with other conventional casting techniques, benefits such as high accuracy, production efficiency, and material-specific qualities can be achieved in Pressure Die Casting. Understanding these differences is crucial for industries seeking cost-effective and high-quality production solutions.