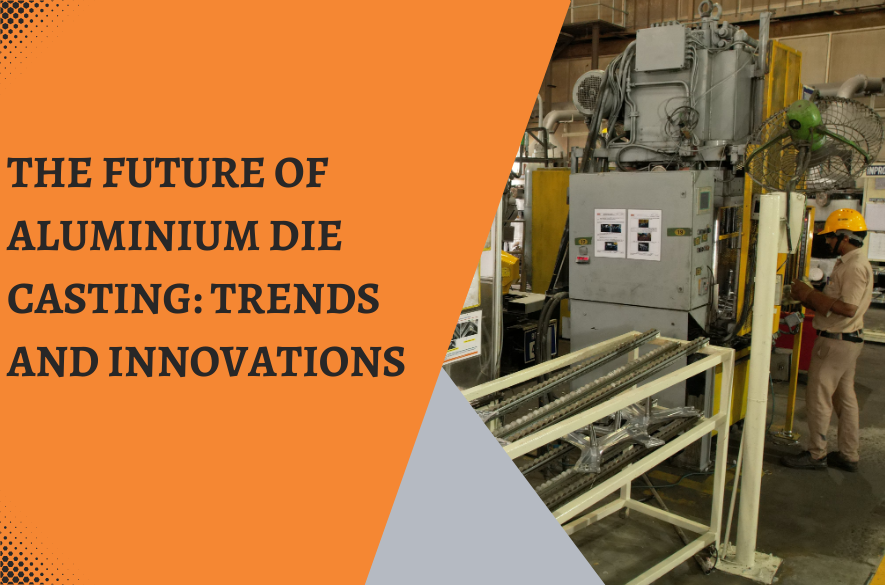
The Future of Aluminium Die Casting: Trends and Innovations
Aluminum die casting is constantly evolving for modern manufacturing and continues to find its application in automobiles, aerospace, and electronics. The reason for this is the increasing demand for lightweight, high-performance materials, where aluminum die casting is making waves, slowly emerging as a vital technology. Here are the future trends and innovations awaiting this industry.
Lightweight and Sustainability
Among the main factors of progress in aluminium die casting is lightweight, driven mainly by the automotive sector. Together with the rise in electric vehicles (EVs) and strict emission norms, automotive manufacturers are keen on aluminium since it is lighter but strong and durable. Aluminium is not only lightweight but also has better corrosion resistance, which makes it one of the sought-after materials for industries today that strive for sustainability. It also allows the recycling of aluminium scrap to minimize waste and conserve resources, which enhances sustainability. Aluminium die-casting manufacturers are increasingly looking out for components to reduce the weight of vehicles without compromising on their strength, and this is expected to be the norm in the forthcoming years as well, as aluminium die-casting companies work to balance performance as energy efficient along with environmental responsibility.
Automation and Smart Manufacturing
The next area of difference can be seen through the advances in automation and smart manufacturing in the aluminium die casting course. Robots and artificial intelligence are increasingly being used in die-casting practices to improve performance, results, and accuracy, as well as reduce humane errors. By using automated systems, the condition of a die-casting machine can be observed in real-time scenario allowing us to achieve precision in every single cycle time and produce consistent and high quality products. Automation increases efficiency and production rates for aluminium die casting companies, further reducing their overall downtime. It has also been helpful in dealing with the increasing need for customization that aluminium die-casting manufacturers face since automated systems allow us to be agile and meet different production specifications.
3D Printing
Another new technology that can be used in die casting is 3D Printing. Traditional die casting uses a permanent mould made from tooling; this is expensive and needs to be made in metal, and these tools need to be maintained regularly. 3D Printing allows for the production of complex parts within hours or days, which is basically a one-off cost, allowing shorter lead time and lower costs. This is particularly suited to aluminium die castings of small intricate components such as electronics and medical devices.
Advanced Alloys and Material Science
As aluminium die casting companies are pushing to innovate; they are also looking into advanced aluminium alloys with superior mechanical properties that are able to withstand higher temperatures and have even better corrosion resistance, hence making them applicable for extreme operating environments such as aerospace and marine industries. The development of these advanced materials is literally increasing what aluminium die casting can do, making it a more and more versatile option for many different industries.
Conclusion
The future of aluminium die casting is bright, with advancements in sustainability, automation, 3D Printing, and technology promising to increase the efficiency, effectiveness and adaptability of the process. Along with the manufacturers embracing these trends, a huge role is set to be played in mapping the future of manufacturing, offering lightweight, durable, and environment-friendly solutions for the usage of multiple industries. Aluminium die casting companies, however, staying ahead of the curve with these developments, are primed and ready to fulfill the changing requirements of the modern industry and thus stay competent in the fast-changing global market.