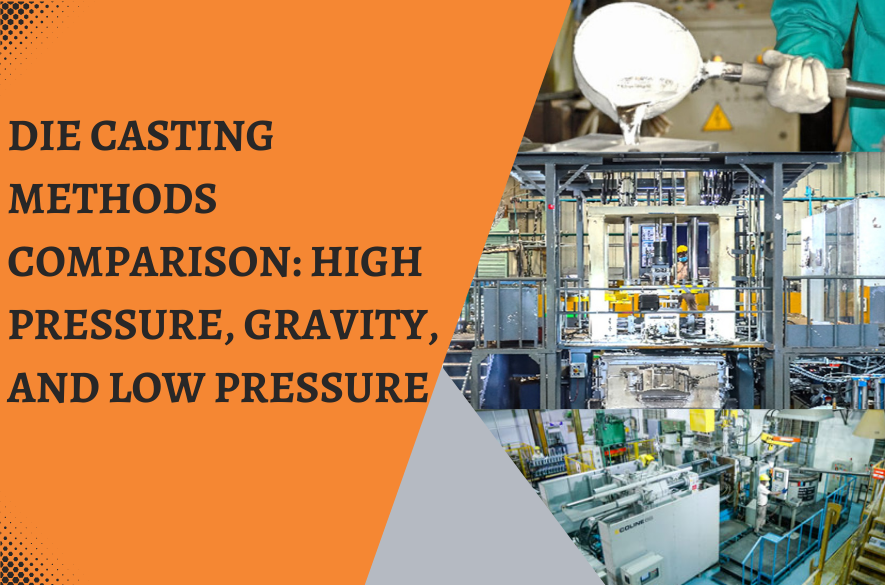
Die Casting Methods Comparison: High Pressure, Gravity, and Low Pressure
In the manufacturing sector, die casting is an essential procedure, particularly for precisely and consistently creating intricate aluminum components. As a Leading Manufacturer of die casting components, meeting the various demands of our customers and optimizing production, all depend on our ability to comprehend the subtleties of different die casting techniques. The three main die casting techniques are High Pressure, Gravity and Low Pressure and it will be covered in detail in this blog, along with it’s distinct benefits and uses.
Overview of High Pressure Die Casting:
The process of High Pressure Die Casting (HPDC) involves injecting molten metal under high pressure into a mold cavity. Rapid injection and solidification are characteristics of this technique, allowing for the production of high volumes of parts with excellent surface finish and dimensional accuracy.
Benefits
- High Production Rate: With a daily manufacturing capacity of thousands of parts, HPDC will be the perfect process for mass production.
- Better Surface Finish: Less post-processing is enough since high pressure guarantees smooth surface finish.
- Dimensional Accuracy: Accuracy of HPDC qualifies it for components that need to adhere to strict standards.
- Material Efficiency: This process is economical because it generates less metal waste.
Applications: In the automobile industry, HPDC is extensively utilized for producing engine blocks, gearbox housings, and other parts that need to be extremely precise and strong. Although HPDC has many benefits, it is not without limitations. Low-volume production might not be appropriate due to the complicated machinery and high initial cost of die fabrication. Additionally, non-ferrous metals such as zinc, magnesium, and aluminum generally react best with HPDC.
Overview of Gravity Die Casting:
Molten metal is poured into a mold cavity using gravity process called Gravity Die Casting (GDC), commonly referred to as permanent mold casting. Compared to HPDC, this technology is more user-friendly and does not require high pressure.
Benefits
- Lower Tooling Costs: Compared to HPDC, the GDC molds are simpler and less expensive to make.
- Versatility: A wide range of metals, including copper, aluminum, and their alloys, can be used with GDC.
- Better Mechanical qualities: Components with slower cooling times typically have better mechanical qualities.
Applications: In various industries, Gears, Engine Parts, and Structural components are commonly produced in medium quantities using GDC. Because this method is suitable for applications where durability and strength are essential due to its ability to produce parts with enhanced mechanical properties. It should be noted that Gravity Die Casting is slower than HPDC and might not be appropriate for extremely large production runs. In comparison to HPDC, the surface smoothness and dimensional accuracy are also usually inferior, which frequently calls for extra machining.
Overview of Low Pressure Die Casting:
Low pressure die casting (LPDC) is the process of pumping molten metal into a mold from a sealed furnace and the pressure holds the metal in the die until it’s solidifies. This regulated procedure ensures steady mold filling, which can reduce defects and enhance the overall quality of the cast parts.
Benefits
- Decreased Porosity: Parts with lower porosity are the consequence of the controlled pressure, which reduces the chance of gas entrapment.
- Better Fill Control: By providing increased process control over the mold filling procedure, LPDC produces components that are reliable and of a high caliber.
- Flexibility: This process is adaptable and can be used to create components of various sizes and complexities.
Applications: Automotive wheels, cylinder heads, and other items requiring high integrity and strength are frequently made with LPDC. It is useful in many engineering applications because of its exceptional accuracy in producing complex geometries. Points to consider: Compared to GDC, LPDC typically requires more expensive initial equipment, and its processing speed may be slower than HPDC. Nonetheless, the expenditure is frequently justified by the component quality, particularly for important applications.
Selecting the Appropriate Approach
Several parameters, including production volume, material requirements, component complexity, and cost concerns, must be taken into account while choosing the best die casting method. It is crucial for selecting the best type of die casting method that fits the project goal. For high-volume production when high precision and superior surface quality are required, High pressure die casting is the best method.Gravity Die Casting is suitable for medium-volume production with a focus on mechanical properties and cost-effectiveness. Low Pressure Die Casting strikes a balance, offering high-quality components with reduced porosity and good dimensional control, ideal for complex and critical applications.
In summary
Comprehending the variations among High Pressure, Gravity, and Low Pressure Die Casting is essential for streamlining production procedures and satisfying a wide range of customer requirements. Die casting producers may increase component quality, boost production efficiency, and keep a competitive edge in the market by utilizing the advantages of each approach. Selecting the appropriate die casting technique is essential for attaining production excellence, whether the goal is to produce sturdy structural components or high-precision automotive components.